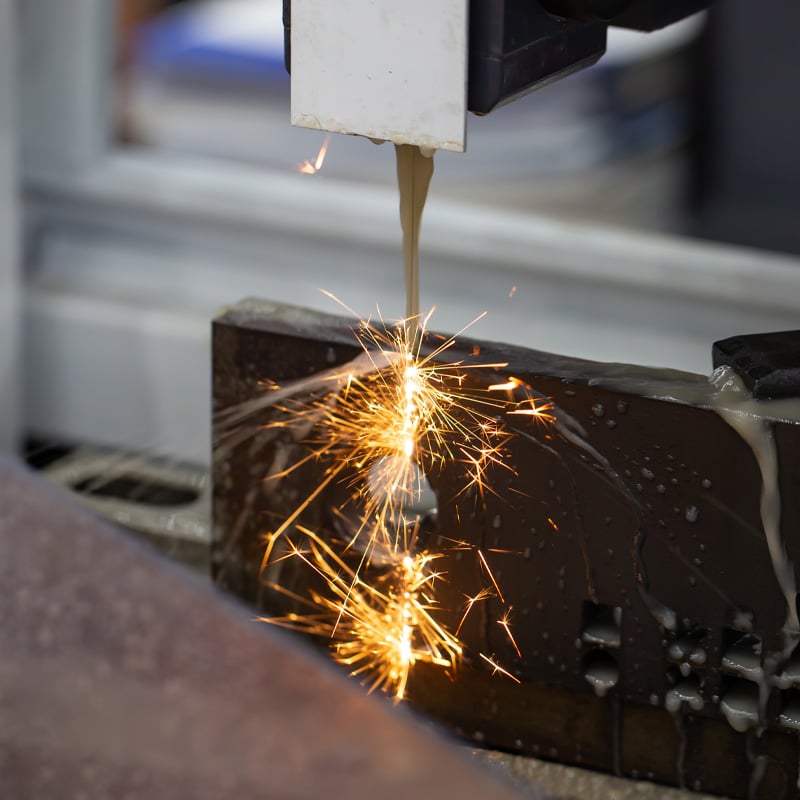
Understanding the EDM Machine Process
The electrical discharge machining (EDM) process relies on controlled electrical discharges between an electrode and the workpiece to shape or cut electrically conductive materials. In wire EDM, a wire electrode—usually made from brass or copper—is charged with high voltage from a power supply. As the wire moves through the workpiece, sparks are generated, eroding the material and creating extremely precise cuts. This process allows for the creation of complex shapes and features that are difficult to achieve with conventional machining methods.
Wire EDM machines use deionized water as a dielectric fluid, which serves to cool the cutting area, flush away eroded material, and control the electrical discharge. The deionized water ensures a stable cutting environment, enhancing the accuracy and surface finish of the machined parts. The cutting speed and intensity of the electrical discharges can be adjusted, enabling the production of components with tight tolerances and high precision. This makes the EDM process highly effective for projects that require intricate detailing, such as in wire harnessing or electrical wiring applications.
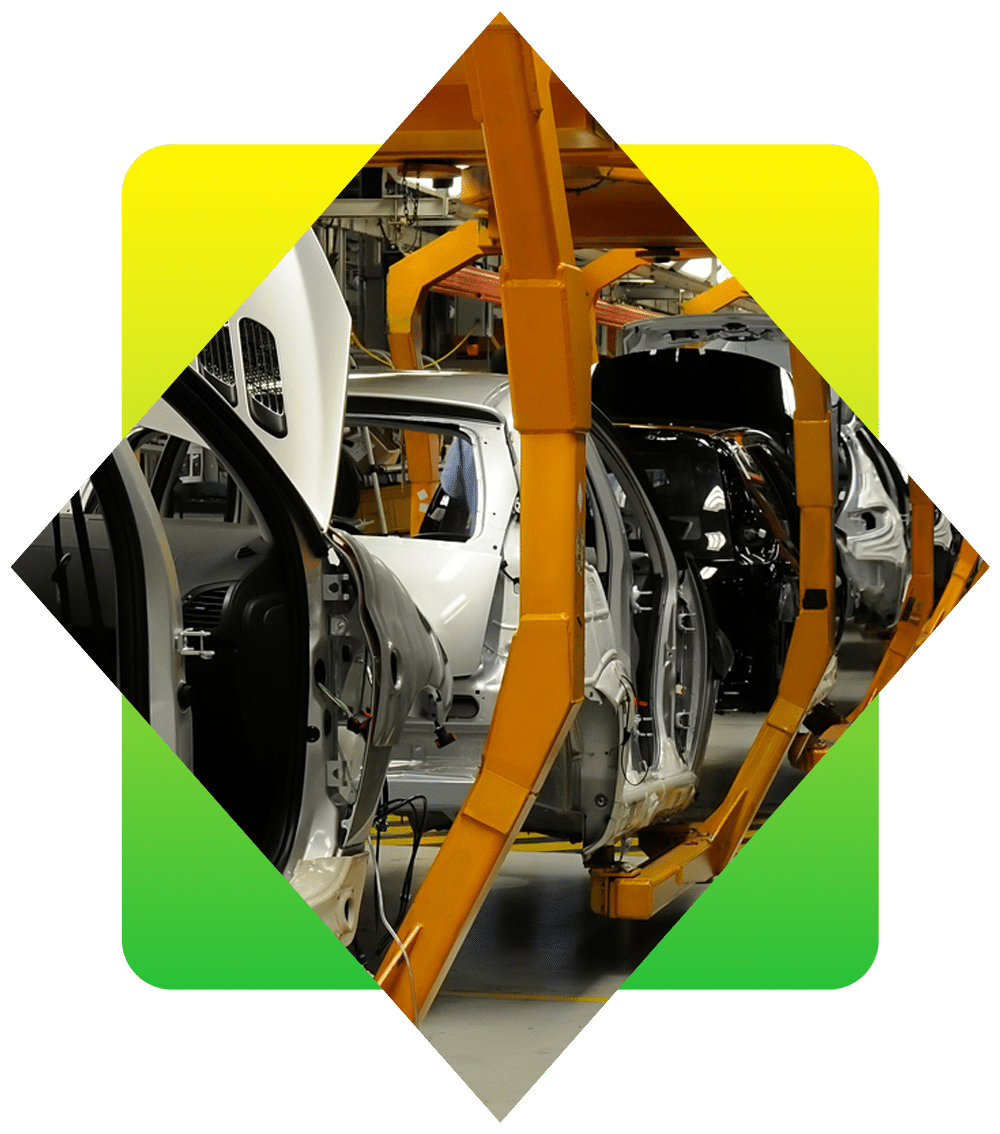
Industries That Benefit from Electrical Discharge Machining
The electrical discharge machining EDM process is widely used across various industries due to its ability to machine complex shapes with high precision. The automotive industry, for example, benefits from wire EDM when producing intricate engine parts and components that require exact specifications. The aerospace sector also relies on EDM to manufacture turbine blades, fuel nozzles, and other critical components, where tight tolerances are crucial.
In the electrical and electronics industries, EDM is essential for creating detailed electrical wiring and wire harnessing components. EDM can machine parts with high precision and complex shapes, making it very important for the production of tooling to form terminals and generate solid interfaces for wire and cable.
The medical device industry also utilizes EDM to produce intricate surgical instruments and implants, where accuracy and precision are paramount. Diamond Die & Mold’s expertise in the EDM process allows us to cater to a wide range of applications, ensuring high-quality results for all your machining needs.
EDM FAQs
Lastly, hole drilling EDM is used to drill small, precise holes in hard-to-machine materials, allowing for accurate machining even in tight spaces.
Additionally, wire EDM can cut with incredible precision and handle intricate designs, such as parts with tight tolerances, making it a preferred choice for industries that require complex, high-precision machining.
The versatility of the EDM process allows it to work on materials that would otherwise be difficult to shape using conventional machining methods, making it ideal for industries like aerospace, automotive, and medical, where complex shapes and exact specifications are required. Whether you’re working with wires and cables or intricate components, EDM provides the precision needed for accurate results.
The constant monitoring of the electrical discharges allows the wire cut EDM process to achieve tight tolerances, making it suitable for applications that demand intricate detailing, such as manufacturing parts for automotive and medical components.
Whether you need delicate, complex shapes for small or larger components, more substantial parts for industrial applications, EDM can deliver high-quality results with consistent accuracy and tight tolerances, making it an ideal choice for a variety of manufacturing needs.
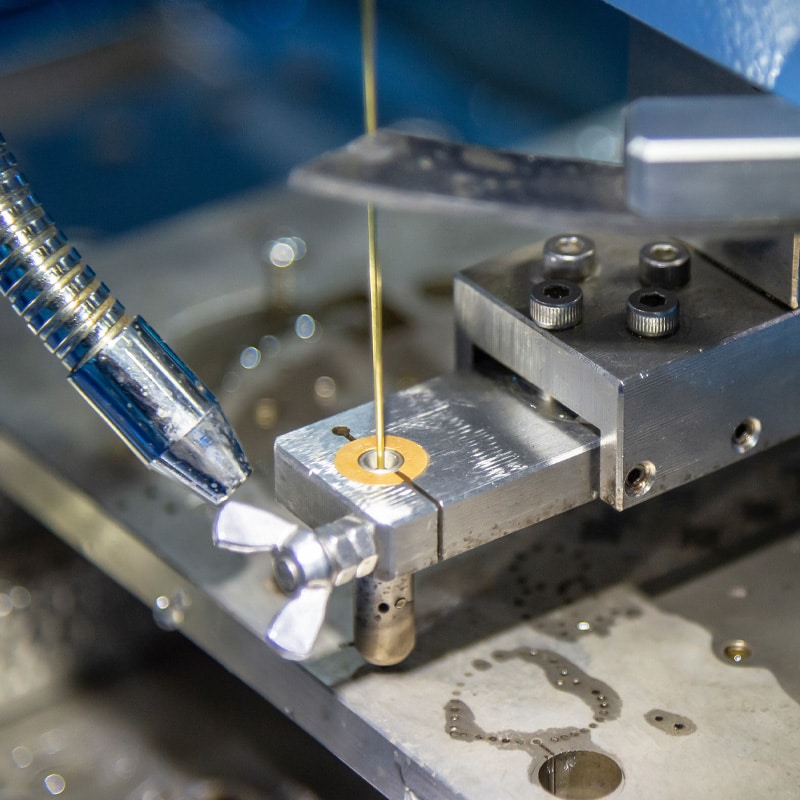
Contact Diamond Dies & Molds for Electrical Discharge Machining Services in Clinton, MI
For expert electrical discharge machining (EDM) services, including wire EDM and hole drilling EDM, trust Diamond Die & Mold in Clinton, MI. Our team delivers high-precision solutions for all your complex machining needs. Contact us today to discuss your project requirements and discover how our EDM expertise can benefit your business.